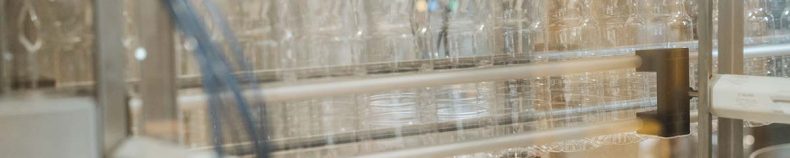
International Asset Management: Burg Group relies on McMain
“McMain is the base on which our machinery is maintained”
Burg Group is a sustainable producer of natural vinegar and tasty syrup. The family business operates globally and has been around for 75 years. It supplies retail organizations as well as food producers and consumers. They produce from 6 locations in 5 different countries. The Technical Departments of the various branches have been working with McMain for 5 years, the last year of which with McMain Online.
“All of our locations now work with McMain Online. As a result, we can now register all our maintenance digitally and optimize processes,” say Marc Hoetmer (Head of Technical Services) and René Kok (Technical Supervisor), who talk about the benefits that McMain Asset Management software offers to Burg Group.
Paperless and time-saving
“We want a paperless factory,” says Marc, “Everything that is currently submitted manually must be registered digitally. McMain is a great tool for that purpose. The software works easily and supports our preventive maintenance perfectly. It ensures that our entire machine park is registered, and that all data about a machine is easy to find. Faults are reported immediately and the status of machines is clear at a glance.
This is of great added value, especially now that there is a lack of technical people on the work floor, but also during the holiday periods, when there are fewer people around. Our summer stop usually lasts 2 weeks. During those periods, maintenance may be carried out by an external technician who has not seen the machines before. All the more important to have the information about the machines digitally in one place.”
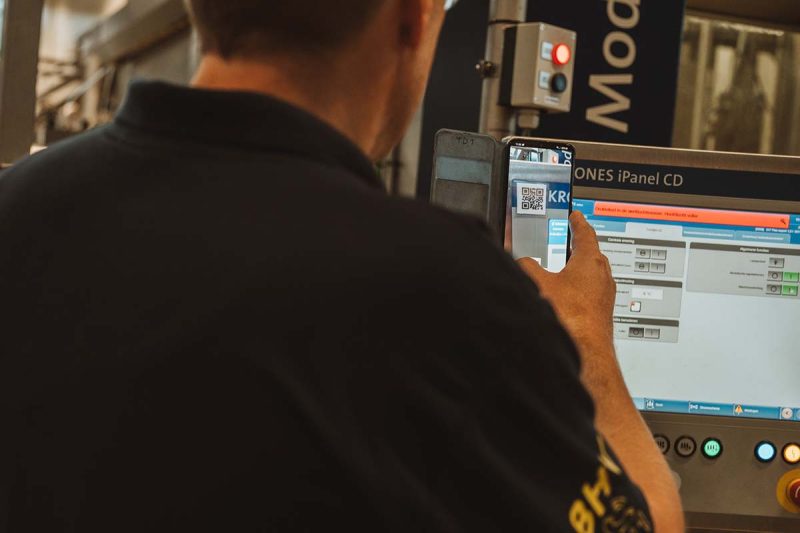
Information for audits readily available
“Preventive maintenance is what we use McMain for the most, but being able to easily provide all the data needed for an audit is just as important.
Because we are private labeled, we have to deal with audits quite often. We get an audit for just about every supermarket. Today’s supermarkets also require you to be qualified to the highest levels, such as BRC and IFS. That means they come by at least every year and also often in between, unannounced.
“In all of our international branches, we pass audits thanks to McMain”
During the audit, they look at how your maintenance is arranged and how you respond to certain risks. In addition, you must demonstrate what your preventive maintenance looks like and where the documentation of your machine park is located. Because we have stored everything digitally in McMain, we can display the information digitally quickly and easily. That’s really the strength of the maintenance software.”
Decline in the number of failures
Marc is very pleased with McMain’s ease of use: “The advantage of McMain is that the program itself indicates when preventive maintenance needs to be performed. This way, work orders are scheduled and not forgotten. Because our machines run a lot, it is important that a malfunction is resolved as quickly as possible. We can’t let a machine be down for some time and continue production on another line. Ad hoc responses used to happen a lot, but since we work with McMain this occurs far less often. We can see a decrease in the number of failures. In fact, we expect that we will have 60% fewer unplanned stops by using McMain!”
“We expect to have 60% less unplanned stops by using McMain”
The insights McMain offers go beyond just maintenance: “Each machine has its own cost center. This allows us to see the cost of each machine at the end of the year so I can make my budget accordingly. This helps us to get the best possible return on investment from our machine park, which is of course what you ultimately want. Additionally, we also use McMain for preventive maintenance for other equipment, such as air conditioners and gutters.
Some OEE software only includes your lines, but this is often only 40% of your factory. We can register all equipment in McMain. And we can therefore also provide a complete overview. It is a great advantage that you have this history immediately at hand, for audits for example.”
The production department feels heard through McMain
Marc and René are also enthusiastic about the speed, ease and transparency with which malfunctions can be dealt with: “The operator can scan a QR code via his mobile phone and immediately report a malfunction. As a result, the report is immediately well documented. If the report is picked up, the operator will also receive a response. This way the production knows that they have been heard. This creates synergy between TD and production.”
But it doesn’t stop there: “Even our CEO can make a report. More than half of the people working in our factory have the app on their phone. This provides a platform for anyone who wants to say something. The QR code on the machines is ideal: it allows you to send a message with just a few clicks. In addition, everyone enjoys working with the app, which is also a huge advantage.”
Always great support. Also international
McMain operates on 6 sites of Burg Group: in the Czech Republic, France, Belgium, Germany and at 2 locations in the Netherlands. “We’ve been working with McMain Online for a year now, on our international sites. This means that the software of the various plants is the same, but everyone has their own database and language. We are well supported by McMain, not only in the Netherlands, but also abroad. For example, one of the consultants recently visited our office in France for on-site training.
Marc keeps thinking ahead and already knows what else he wants in the future: “The next step is predictive maintenance. We will make this step once we have planned maintenance under control. We also have plans to link OEE and MES systems to McMain. This gives us even more insight and means that the technicians have even less registration burden.”
The ultimate goal for using the maintenance software is maximum deployable machinery: “McMain helps us to create an overview. We sometimes change machines, and machines sometimes change locations. When that happens, it is ideal that you have access to all information and data from a machine.”
Want to try it out for yourself?
Want to get started with McMain Asset Management software? Then Marc recommends the following: “Make sure you give yourself enough time to set up and maintain the system. It takes time, but it also pays off. So plan plenty of time for this.”
Do you have other questions? We are happy to talk to you. Feel free to contact us via [email protected] or +31(0)341 – 750 500.