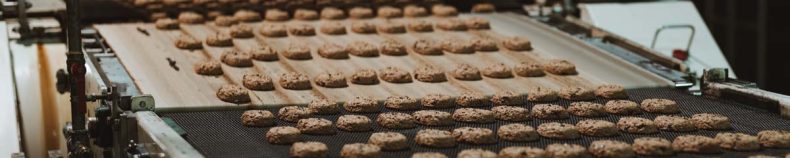
Van Delft Biscuits
“McMain fits perfectly within our philosophy”
They are a statement in the Netherlands, the gingerbread biscuits of Van Delft. The company based in the city of Harderwijk is the creator behind these much beloved biscuits. At their production site, they use up to eight production lines to meet the demand of supermarkets in the Netherlands as well as abroad. Nico van Nieuwenhuizen, who works within the technichal department of Van Delft tells us about his experience with McMain.
Even though the demand amongst consumers for the gingerbread biscuits is mostly focussed around the holidays season, production already starts in april. In order to meet the massive demand, it is important that the production starts well ahead of the season. By doing this, Van Delft is able to create a buffer for when the season starts. It is a well known fact that that Van Delft serves whole of the Netherlands with their gingerbread delights. Whats is less known however, is that Van Delft is the biggest gingerbread baking facility in the Netherlans. And with this title, there is always something to do inside the factory.
‘The bible for failures and maintenance’
Eight production lines equals eight times the risk of downtime. Therefore Nico and his team fullfill a very important job when it comes to the production of Van Delft. “The maintenance software of McMain has become irreplacable within our team. We have been using the software for a couple of years now, on a daily base. We call it our bible for failures and maintenance” Van Nieuwenhuizen continues: “We as the technical department work closely together with the line managers. If any problem occurs, they are the one who signal us by entering it in McMain. By completely digitalizing this process, we are saving a lot of time on unnecessary conversations. We use a certain kind of philosophy when it comes to the acceptance and resolvement of failures on our lines. McMain is able to streamline this process for us in their software.”
Audits and the role of McMain
“When one of the line managers signals a failure in the software, he will be kept up to speed on the status of it, just by looking in the software. We also generate a report twice a day, which keeps us informed about the daily activity. This information we can share with the rest of the company” “Within our organisation, certificates play an important role. McMain assists us in documenting our certificates. This way, we dont have any problems during audits, because all the documentation is in the right place. McMain is an absolute improvement on our previous system, which consisted of registration on paper. But that doesn’t belong in the 21st century anymore.”
“Within our organisation, certificates play an important role. McMain assists us in documenting our certificates.”
Acting instead of reacting
The main goal of Van Delft, when it comes to maintenance, is acting instead of reacting. In order to achieve this, the registration of failures plays a important part to help make data driven decicions. “Last year we registered about 80-90% of our failure in McMain. This gives us alot of insights about our current situation ‘What happened’, ‘what are the sore spots within the company?’, these are the most important questions on which we can now give well-grounded answers. And these answers will help us improve the uptime of our lines.”
‘Addition to the company’
“The support of McMain is very good. Whenever we ask a specific quesiton, they will have the answer in no time. Also when adjustments are needed to reports for example, they will create it in no time. When it comes to that, they are like wizards. But also in general, the hospitality and service of McMain is very good. And when McMain is carried troughout the whole organisation, it realy is an addition for everyone.
Get started
Do you want to see how McMain can help you? Start with your free trial of McMain Online