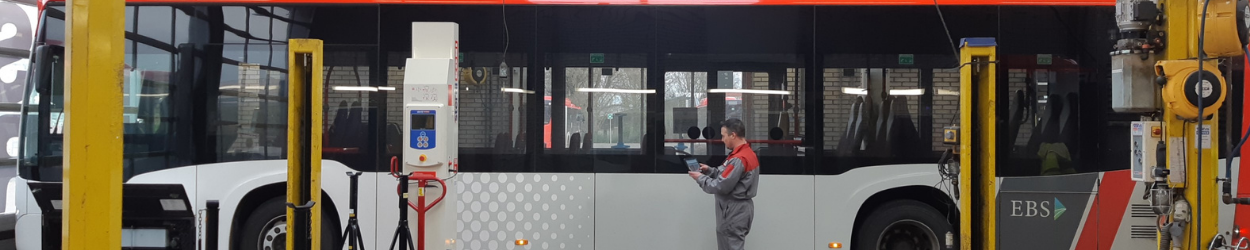
EBS Public Transportation B.V.
“Thanks to McMain we have insight at mechanic, workshop and bus level”
An ambitious public transport company, where the passenger and the quality of the journey are a priority. That is how Frans describes the organization he works at. To get to that perfect travel experience, good material is a requirement and that is when McMain comes into the picture. Frans ter Beke, Delivery Manager at EBS Public Transportation B.V., talks about his McMain experience.
Frans has been working in the world of public transport for twenty years and he knows like nobody else what is needed in order for the implementation of a maintenance application to be successful. “I had a déjà vu with my first project in 1999, also in the workshop. It is always uncertain how technology and automation is received within a team, like the Digital Technician. It does lighten the administrative load; the most important thing is having everyone on the same page so the acceptance rate is as high as possible.”
Searching for maintenance software
“EBS has grown a lot in the last two years and that is why you can see that some processes need to be reassessed. This was also true for the workshop and we saw that the maintenance package did not fit anymore with the current ambitions. That is why we went looking for a replacement. We are a relatively small organization, but we do our own maintenance on different kinds of buses. So it was important that we record all these different suppliers in the system. That is how we arrived at McMain. I contacted them and liked the service and offered functionalities so much that we immediately joined forces with McMain.”
Lightening administrative load with the Digital Technician
“Where we would previously be able to take a walk to get information, with four different locations this has become impossible. So we had to make sure that we could collect and access our information in another manner. This is where a bit of efficiency comes into play, because we want to simplify the processes of the workshop. This is where we took some steps, because we started using the workshop software from McMain, but also with the introduction of the Digital Technician. The best part is seeing how enthusiastically this tool was received by the technicians, because an enormous administrative load disappeared. We are working on collecting the data and next year we will start using these data in a Power BI tool. The foundation has been laid, the first steps have been taken and it is alive and well among the EBS staff.”
“Thanks to McMain we have insight at mechanic, workshop and bus level, so we can work more cost efficiently.”
Management of costs
Besides working efficiently and lightening the administrative load, another element was important in the decision to switch to another maintenance program: cost management. “In the past, it was commonplace to divide the total maintenance costs by the amount of buses to get to an amount per bus. The EBS workshop was in essence one big black box with no insight in the expenses. There were checks to see if technicians recorded their hours and the warehouse value was monitored; but that was it. Nowadays that is unimaginable. We are in the middle of a transition to working more data driven and we want access to information on the technician, workshop and bus level. Think about mutual cost differences, costs per bus, where are the expensive parts used and which materials are wasted? That is how we can work more cost efficiently.”
Goal for the year: getting the warehouse in order
What do EBS want to focus on in the short term? “The warehouse”, answers Frans. “At the moment that is an area where a lot of value is still on the table and that is what we are employing the Digital Technician for, because with it we can scan barcodes. This requires discipline, because if the technicians get material for a work order, it has to be scanned. We hope the warehouse is up to date and the workers can always find what they are looking for. The goal is to get insight in the expenses, but also the warehouse mutations and the differences. Personally, I think this will work, because they will see this as a solution themselves, so the acceptance rate will be high.”
“Sit down with people who think in processes and are change-minded.”
Tips for starting with (workshop) software
We look back at the starting phase that EBS had with the workshop software and what tips they want to give other starting organizations. “Sit down with people who think in processes and are change-minded.” There a major role was played by Gert ter Burg, the functional manager, who also has a lot of experience in public transport. “This way, you can start quickly and take steps with the maintenance software within the Technical Service. And put the processes on paper, so everyone has it clear in front of them and then you can say: this is how we are going to do it. What I personally think is important, is good cooperation with the partner and I think that in McMain we found a partner who, like us, wants to enter into a long-term relationship characterized by regular contact and the possibility of discussing all matters.”
Start now
Do you also want to start using maintenance software after reading the customer experience of EBS? You can trial our software 30 days for free. If you have any questions, feel free to contact us at [email protected] or +31 341 – 750 500.